Japanese Workplace Culture VS. American Workplace Culture
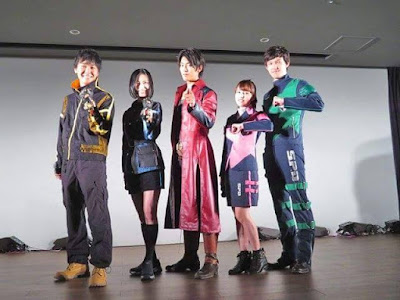
It's no secret that Power Rangers' quality has been declining at a very rapid rate. I decided to read through some of the differences between Japanese work ethics and American work ethics to write this post. This would probably help me get a picture of the possible work ethic that the companies involved namely Toei Ltd. and Bandai Japan may greatly differ than that of Saban Brands and Bandai America. After writing about the big difference in innovative thinking between the two franchises - now it's time to compare Japanese workplace culture vs. American workplace culture.
I. Worker characteristics and their attitude towards work
The typical Japanese self-image is focused on belonging to a group. It's okay to show feelings and weaknesses. This is not a part of some stupid macho culture where men are taught not to cry. They believe that people belong to a group. While they respect individual differences and require individual contribution but the group must first succeed for any contribution to have meaning. The American self-image is very individualistic. It's the macho culture where you can't be allowed to show weakness. That alone is a cause to why weaknesses tend to surface a lot in Japanese culture.
There's a big difference with how Japanese and Americans view teamwork. The Japanese don't believe in the use of star players and everyone must cooperate. They believe that while competition is important but a team must work as a team. The American culture uses political power plays to become stars. Getting someone to stand out may instead be the person who outdid the others than the one who brought the others together. From observation, it seems that the American concept of teamwork tends to have people drag their teammates down so they get all the credit.
What I also like about the Japanese over the American is their attitude towards authority. Is it me or is America today filled with more people having a very substantial view of authority than those who don't? I could be wrong in that assumption though. You can observe the orderliness of how schools and community differ in their attitude towards authority. If you have people who have a high regard of authority then you have employees who are willing to comply with the work required of them.
The typical Japanese have a high attitude towards work. They practice self-discipline, they live to work and they ask what they can do for the company. They are willing to put aside their personal stuff to get the work done. The typical American problem with work is that they tend to work to live, self-gratification and asking what the company can do for them instead of what they can do for their company. So much for JFK once saying to them ask not what their country can do for them but what they can do for their country. Having a low tolerance for personal discomfort is never good for the work environment.
It can be seen how typical Japanese don't have the haciendero mentality or where they expect others to do the cleaning for them. They teach their children to clean up the place and do the work themselves. Being a janitor is not a degrading work for the Japanese. You may even see your superiors clean up his own work place or ride the bus without hesitation. Typical Japanese also have a very high respect for other people's property.
II. Management polices and attitude towards subordinates
It's true that bosses call the shot but they are not bosses if they have no subordinates. Typical Japanese have the kaizen attitude which is all about using workers' suggestions and participation in order to achieve continuous achievement. This is all about getting feedback, taking them with a grain of salt to see which one works and which one doesn't work. On the other hand, the American system seems to view feedback from subordinates as a threat. There's always such a thing that you may be the leader but your job is to influence but not to know everything. If you don't know anything about what your subordinates think then how can you find creative ways to lead people?
Training is a very important thing for everyone. Without training one's abilities how can there be improvement in them? Its absence can eventually lead to them rusting. The typical Japanese way has a high commitment to training to make sure employees become more competent. They use cross training methods where people are allowed to experience what others are doing. It's letting everyone have a bigger idea of subjects beyond their expertise. The problem of the typical American way is that they have very little commitment to training. Having a lack of training many explain why America is now so downward with incompetence. By scavenging workers they may have allowed even incompetence to grow.
Motivation and rewards really go a long way don't they? The typical Japanese way is focused on recognition, pats on back, trophies, tokens of appreciation and profit sharing. This may be all about getting your recognition not by derailing the whole group but by bringing the whole group together. You have charts or boards over work stations to show goals and current state of achievement to see how everyone did and how one can improve in group cooperation. Meanwhile, the typical American is only focused on monetary and ego. If people are only focused on self-inflation then the motivation for reward only leads to destroyed teamwork.
Having a boss who's accessible to workers is important. If the managers' office is at the plant then he or she can see better of what's going on. He or she can address problems better. The problem of not having your manager see the situation is bad. How can he or she address the problems if he or she is aloof? That wouldn't be good to addressing problems wouldn't it?
III. Management's competitive focus and policies
Quality planning is very important. Innovation involves four Ds namely definition, discovery, development and delivery. If your innovation doesn't deliver the intended results then it's time to learn from that mistake and make sure it delivers better results. What's the huge issue of quality planning? Nobody should be okay with that will do or the mediocre mindset. Instead, people should be more focused on kaizen or continuous improvement. It's because in the world of competition the only way to survive is through proper use of innovation. Innovation means coming up with new ideas though it's not enough. It's not just introducing change but making sure that change delivers good results.
There is the difference between short-term planning and long-term planning. The typical Japanese and typical American view on innovation can be shown. The typical Japanese have a long-term view on overall focus and operating strategy. They continuously innovate since the long range focus is on competitive strategy and continuous improvement of operations management. Innovation would seek to keep working long term that it continues to define, discover, develop and deliver. Innovation that relies too much on short range thinking and fixed set of constraints may sooner or later end up riding on past successes.
The inventory and waste management system really matters. I noticed how often I hear of typical Americans tend to throw away leftovers when they could still be eaten in good condition for the next day. Typical Japanese tend to utilize the resources as much as possible. Typical Japanese use the Just In Time and Just Enough Resources by making sure that while there's allowance for excess but not too much excess. Minimum workers must be highly skilled and flexible in what they do. The typical American way have too much Just In Case in their inventory which may explain why some are idle (because they have nothing to do) while other resources suffer depreciation as a result. Worse, they have the dehumanizing repetitive tasks which may also explain why some schools today may be making people stupid about real life decisions.
The Japanese quality control uses Total Quality Check. There should be zero defects and it should be used as a strategic weapon. The typical American inspects for optimum level of defects. This may also be connected with how equipment is treated. Typical Japanese tend not to overuse and abuse their equipment as much as the Americans. While the answer lies in the hand and not in the blade but a defective blade can also be the cause of one's defeat. Having habitual maintenance is all about prevention is better than cure. The problem of waiting until equipment breaks before it's replaced can eventually cause a slowdown in the work process together with a drop of quality in the long run. Typical Japanese production practices focus on specialization while typical American production practices have less focused plants.
IV. Management accounting and control
Overall reporting strategy in the typical Japanese way is to influence behavior. It's not just about the money but also strategies. The typical American way is to inform management only with quantitative means. It would be important to consider how behavior is influenced and it's not just enough to inform management. The typical Japanese planning and control is bottom up, goal setting and feedback, worker participation involved with long term planning for long term. The typical American is top down, rolling down financial budgets to lower levels and based on engineer driven standard costs only which is usually focused on short term.
How the typical Japanese firm and the typical American firm views Return on Investment (ROI) shows a big difference. The Japanese view of ROI emphasizes on the means to get to one's big profit. A good example would be evaluating how to create the process and how money can be achieved. On the other hand, the typical American firm may think like the Krusty Krab on ROI. They tend to only care about the end result than how it's achieved. In short, it's all about short-term thinking where you want your money back now. It's not just getting the money back but also making sure you have a sustainable plan to continue the cash flow. It's like you don't poison rivers and cut too many trees so in the future both the rivers and the trees will continue to generate money that can be enjoyed for the future generations.
The typical Japanese have measurements based on life cycle costs, quality, lead time, flexibility (e.g., average number of jobs mastered per employee, average setup times) number of line stops, down time, process times, amount of inventory and number of customer complaints. This is a very detailed way of doing things. The typical American system is just too focused on cost variations, labor efficiency, machine utilization and meeting due dates. One should note that being efficient and being effective are two different things. Efficiency is getting the work done on the desired time. Effectiveness is whether or not something achieves the desired result.
References for further reading on work culture differences:
Martin, J. R., W. K. Schelb, R. C. Snyder, and J. C. Sparling. 1992. Comparing the practices of U.S. and Japanese companies: The implications for management accounting.
Comments
Post a Comment